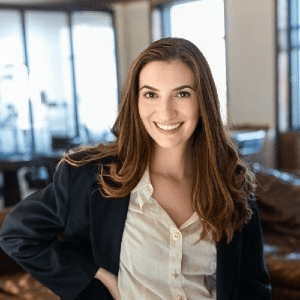
Emily Newton
Original equipment manufacturer (OEM) casting requires precise steps to get parts that match exact specifications. However, digitalization in die-casting industry processes is gaining momentum, enabling users to have tighter quality control, better visibility, ecommerce opportunities, and other benefits. Here’s a closer look at some of the many impacts affecting the industry.
OEM casting requires constant oversight of various steps that must occur correctly for people to get the desired results. Human supervision is almost always an element, but more casting companies are also letting digitalization play a role. That allows people to be physically away from the location where the casting processes occur but still be aware of everything happening within the facility.
Improved monitoring of complex processes
Consider a case where researchers built a smart manufacturing system in a facility specializing in aluminum die casting for automotive parts. One of the things the team did was learn more about the types of die-casting defects. They also connected Internet of Things (IoT) sensors to get equipment conditions, casting parameters and details about furnace operations.
This study analyzed 96% of factory parts that had the most data available. About 89% of those were for components that passed quality control checks, while the remaining 11% did not. The researchers used that information to learn more about the most important factors that lead to high-quality casting results.
The researchers also planned further work involving creating algorithms to identify the links between casting parameters and a bigger variety of products. Moreover, they wanted to build algorithms that could automatically respond to different process parameters, helping to get the best outcomes.
Many manufacturing analysis solutions operate in the cloud. Authorized users can access them from anywhere and at any time. That makes it easier to see whether specific OEM casting sites meet expected metrics or if there’s substantial room for improvement. Digitalization in die-casting industry facilities allows constant oversight of highly precise processes.
Reduced adverse outcomes due to better proactiveness
High-pressure die casting relies on a hydraulic piston system to put molten metals into a steel cast, resulting in efficiently created parts. Depending on the metal, this process exerts between 3,000 and 10,000 pounds per square inch. Digitalization in die-casting industry steps can allow people to verify everything’s going well. It also lets them spot problems early and take corrective actions.
One example came when people built a digital twin to improve high-pressure die-casting processes. They realized that could allow them to predict distortion caused by earlier steps and adequately correct for it in later stages. The digital twin would help them determine how long to expose the just-casted parts to cooling and minimize distortion in the process.
Those working on this project knew that correcting distortion through secondary means can be prohibitively costly or otherwise not preferable. For example, handling it with mechanical forming requires specialized tools. Thus, they believed the better approach was to predict the outcomes of the casting and heat treatment processes. They’d then use that information to make the necessary cooling process adjustments.
Their results showed this approach is a viable alternative to casting processes that are less or not at all reliant on digitized processes. However, they recognized the need for further research in this area.
Casting professionals can also reduce operational problems by programming IoT sensors to assist with supply reordering. Inventory-monitoring sensors can automatically order products once goods drop below a reorder-point threshold. An even more common scenario is to use sensors on critical equipment. People can get alerts to purchase spare parts or schedule service calls before parts wear out or entire machines fail due to issues humans haven’t spotted.
Enhanced data usage for digitalization in die-casting industry facilities
Many manufacturing companies have access to tremendous amounts of data. However, the leaders at those facilities often need help analyzing it to extract useful insights. People have invested more to achieve digitalization in die-casting industry processes, and many have explored how to harness the power of data analytics.
The successes span beyond OEM casting. One instance concerned creating 30% stronger concrete with data-backed mixture improvements. A compelling reason to use data analytics in casting processes is that specialized platforms can usually handle huge amounts of information much faster than humans.
Toyota used a data analysis tool from Siemens to improve outcomes associated with aluminum die casting used to make automotive air-conditioning compressors. Leaders at Toyota hoped this approach would let them detect process deviations that could lead to product irregularities.
The company used artificial intelligence (AI) and big data analytics to analyze approximately 40,000 data points per die-casting shot. Those checks happened instantly and gave details about the expected quality of the finished component.
Besides significantly improving quality control, this approach allowed Toyota representatives to receive notifications of potential equipment failures and correct them before errors or malfunctions shut down production. People must determine their goals before embarking on data-driven process changes or decision-making efforts. However, these results show why it often pays off to use powerful tools and reveal trends or other valuable information.
Digitalization in die-casting industry operations makes sense
Implementing digitalization in die-casting industry practices takes longer than a few weeks.
However, many leaders find they must do it to keep pace with competitors. Otherwise, process problems could result in defective die-casted parts, wasting time and money. In other cases, people may not detect manufacturing problems until it’s too late, meaning they fall behind agreed-upon deadlines.
Decision-makers should consider what options they want to overcome by moving ahead with a digital transformation. Narrowing down the possibilities will make it easier to identify some easy wins that could motivate leaders to take continued digital transformation steps.
About the author:
Emily Newton is an industrial writer reporting on how technology disrupts industrial sectors. She’s also the editor-in-chief of Revolutionized, covering innovations in industry, construction, and more.
Sign up
Sign up for a complimentary subscription to Digital Commerce 360 B2B News, published 4x/week, covering technology and business trends in the growing B2B ecommerce industry. Contact editor Paul Demery at [email protected] and follow him on Twitter @pdemery.
Follow us on LinkedIn and be the first to know when new Digital Commerce 360 B2B News content is published.
Favorite